Building a Steel Casting Furnace
- muleequestrian
- 1 hour ago
- 2 min read
I decided that I needed to start making some obsolete gun parts that I couldn’t find anywhere else. Sometimes you get an older antique gun in the shop and parts are just not available for it anywhere. I had initially taken blacksmith classes to be able to make gun parts, but sometimes you just have a part that needs to be cast simply because it’s too difficult to machine it from a roughly forged blank.
I started out with an empty propane tank.

I opened the valve to make sure everything was completely drained. Then I used a wrench to take the valve off the tank. I completely filled it with water to ensure that no gas remained inside.

I used my plasma cutter to open the tank at the top seam. I followed the original weld line to make a top lid for the furnace.

This became the body and lid for the furnace itself. The valve protector was cut off next.
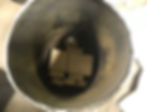
I placed fire bricks in the bottom of the propane tank.

I lined the interior with 2,000*f Kaowool fabric.

The bottom got a layer of Kaowool too.
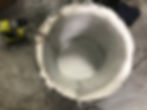
Next came a liner of hardware cloth to help keep the liner in place, and add a bit of rigidity.

A series of holes were drilled to add a pipe to the side as a place to put a Venturi.
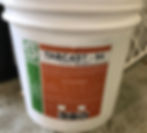
I mixed a high temperature refractory and started building the interior walls.
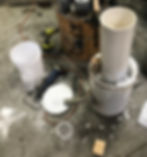
I had thought about adding some stainless steel needles to the refractory as reinforcement, but decided against it since I didn’t want the walls to expand at a different rate and form cracks.

After cutting a form from schedule 40 PVC I prepped the entire furnace body and let it air dry for 2 weeks before I did the intial burn out. If it were possible, I’d have used a cardboard tube it one were available. PVC is really nasty when it burns, and puts out a lot of ashes and nasty black clouds.
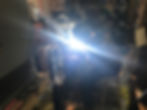
Next, I added a small propane cylinder to the center of the lid that had been cut open on both ends, and welded it in place as a chimney. I also added two pieces of rebar to act as handles for the lid.

I made the lid with a liner just like I did for the body of the furnace.
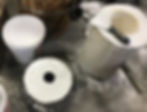
Keep in mind that iron melts and flows at about 2,200*F, and steel needs about 2,800*F. So select the refractory with a high enough temperature rating that doesn’t destroy it at that heat. Tabcast 94 has a rating of about 3,275*F. Castolite is rated at 3,600*F bit wasn’t available at the time.

It took almost a year to research and build this foundry furnace so that it wouldn’t simply burn up at the first use. I had no classes to attend, so this was a learning curve. It’s hardly something you simply build and begin melting and casting steel right off the bat. There’s much more to this than just what is shown in this blog.