Pattern Welded Damascus Steel
- muleequestrian
- Jun 22
- 2 min read
Pattern welded Damascus for knife making is made from two types of material forge welded together. Using high heat and fluxed with borax to prevent oxidation, you use light hammer blows to tack the steel together.
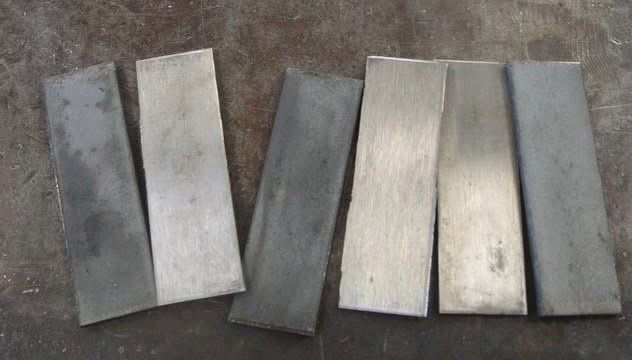
I generally use 1095 carbon and 15N20 nickel steels.
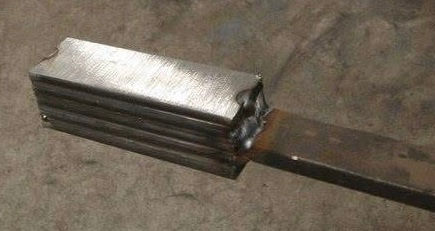
I place the two steels in alternating layers and MIG weld them together into a “lollipop”.
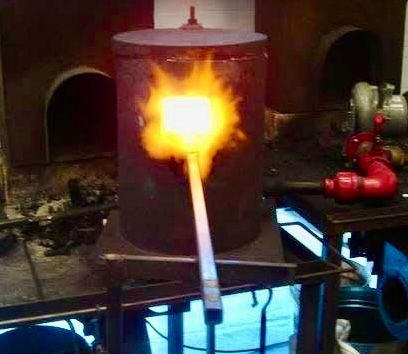
I run the stack of layers in the furnace, and heat it up with a coating of borax to close out the oxygen. Without the flux, you have oxidation and end up with the weld not sticking. This is called a cold shut.
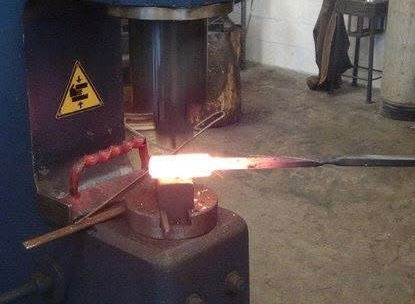
After heating, I run the stack under a power hammer and flatten it.

After heating again, I partially split the bar and fold it over to forge it together again. Each subsequent cut, fold, and reweld actually doubles the number of layers of the bar.
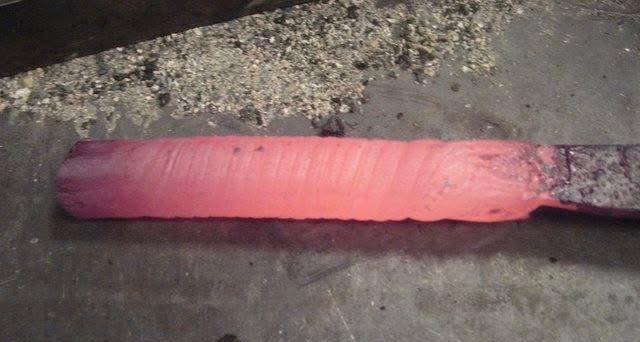
Once the bar is forged round again, you can twist it to create a pattern. Additional patterns can be drilled partially, lines cut vertically part way through, or cut and restacked and rewelded. Depending on how you manipulate the metal in this state, decides how your pattern comes out.

No two patterns are ever the same. Each blade blank is as unique as a fingerprint, but you can definitely make similar patterns.

Ferric chloride etch brings out the patterns very well. The acid turns the carbon steel black and leaves the nickel steels untouched. Other etching can be done with mustard from the kitchen, vinegar, or other methods. I rub baking soda on the blade to neutralize the etchant, and rinse the blank, dry it and oil it lightly until it’s time to grind and turn it into a blade shape.

Different patterns can be made with drilling partially, grinding partial lines, or just twisting.
Comments